High Pressure Die Casting Products: A Comprehensive Guide
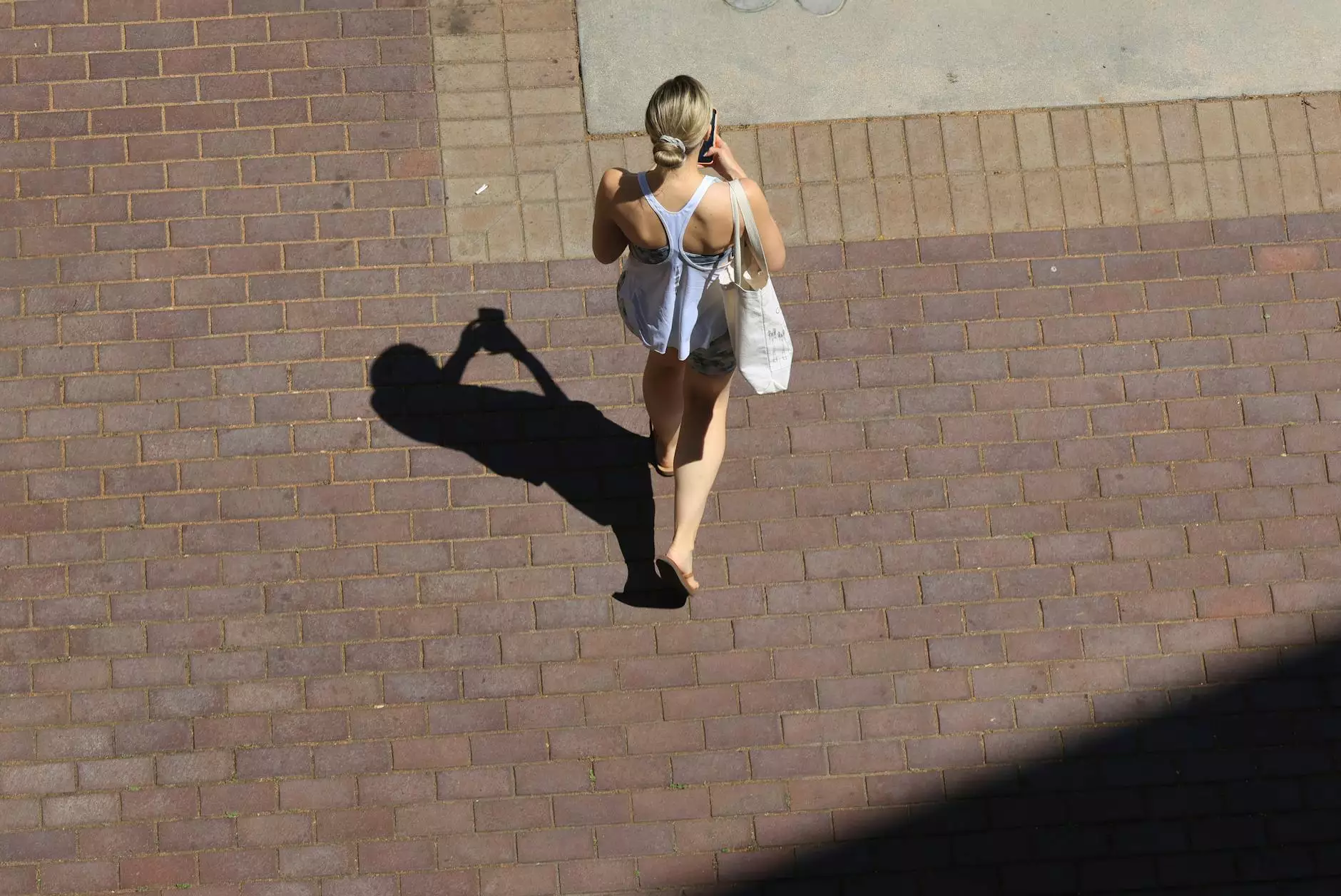
In the ever-evolving landscape of manufacturing, high pressure die casting products play a pivotal role in the production of complex and high-quality metal components. As industries ramp up production rates and demand for precision engineering increases, the use of die casting has surged, making it an essential part of metal fabrication processes across various sectors.
Understanding High Pressure Die Casting
High pressure die casting is a versatile manufacturing process that involves injecting molten metal into a steel die at high pressure. This technique allows for the production of intricate shapes and features that would be difficult or uneconomical to achieve through traditional manufacturing methods.
The Process of High Pressure Die Casting
The high pressure die casting process can be broken down into several key stages:
- Preparation of the Die: The first step involves creating a precisely engineered metal die. This die is made from steel and is designed to withstand the high temperatures and pressures of the casting process.
- Melting the Alloy: Aluminum, zinc, and magnesium are commonly used alloys in high pressure die casting. The metal is melted in a furnace to achieve the desired temperature.
- Injecting the Metal: The molten metal is injected into the die using a plunger mechanism at a pressure that can exceed 1,500 psi. This ensures that every detail of the die is filled.
- Cooling and Solidification: Once the die is filled, the metal is allowed to cool and solidify. The cooling time can vary based on the complexity and thickness of the part.
- Removal of the Casting: After solidification, the die is opened and the casting is ejected. This process can be repeated quickly for mass production.
Advantages of High Pressure Die Casting Products
The benefits of utilizing high pressure die casting products are numerous, making this technique the preferred choice for many manufacturers:
Cost Efficiency
High volume production significantly reduces the per-unit cost of products. The initial investment in die creation is offset by the production of thousands of parts in a consistent manner.
Precision and Accuracy
Die casting provides extremely tight tolerances, enabling manufacturers to create parts that fit together perfectly, reducing the need for post-casting machining.
Complex Geometries
The process allows for the production of complex shapes with fine details that would be difficult to achieve with other methods, such as machining or injection molding.
High Strength-to-Weight Ratio
Die cast parts often have a superior strength-to-weight ratio, making them ideal for applications in automotive, aerospace, and consumer products where weight savings are crucial.
Applications of High Pressure Die Casting Products
The versatility of high pressure die casting products means they find use in a variety of industries:
Automotive Industry
In the automotive sector, die casting is used to manufacture components like engine blocks, transmission housings, and other critical parts that require not only strength but also lightweight properties.
Aerospace Sector
Aerospace applications demand high precision and reliability, which die casting can achieve. Parts used in aircraft and spacecraft often benefit from the reduced weight and increased durability provided by die casting methods.
Many consumer electronic devices utilize die cast parts for enclosures, frames, and other structural components, allowing for sleek designs that do not compromise on strength.
DeepMould.net: A Leader in High Pressure Die Casting
At DeepMould.net, we pride ourselves in being at the forefront of high pressure die casting technology. Our commitment to quality and innovation has made us a trusted partner for businesses looking to achieve excellence in their manufacturing processes.
Our Expertise
With years of experience in metal fabrication, our team of experts ensures that every product meets the highest standards of precision and quality. We utilize the latest technologies in die casting to deliver products that not only meet but exceed our clients' expectations.
Quality Assurance
Quality is paramount at DeepMould.net. From the selection of raw materials to the final inspection of die cast products, we adhere to stringent quality control measures to ensure reliability and performance.
Tailored Solutions
We understand that each client has unique needs. Our tailored solutions in die casting allow for customization in design, material selection, and production processes, providing our clients with the flexibility they need for their specific applications.
Future Trends in High Pressure Die Casting
The future of high pressure die casting products is promising, with continual advancements being made in technology and materials:
Increased Automation
As automation technology progresses, we can expect more efficient production lines, reducing labor costs and increasing production speed while maintaining quality.
Sustainability Initiatives
Environmental concerns are leading the way to more sustainable practices in manufacturing. Innovations in recycling metals and reducing waste will play a critical role in the future of die casting.
Advanced Materials
Ongoing research into new alloys and materials will enhance the performance of die cast products, enabling them to withstand greater stresses and temperatures.
Conclusion: The Impact of High Pressure Die Casting Products on Modern Manufacturing
In conclusion, high pressure die casting products represent a cornerstone of modern manufacturing. Their combination of cost efficiency, precision, and versatility makes them indispensable across multiple industries. As leaders in the field, DeepMould.net is committed to providing high-quality die casting solutions that empower businesses to innovate and succeed. We invite you to explore our offerings and discover how we can help elevate your manufacturing processes.
For more information about our die casting services, please visit DeepMould.net.