The Ultimate Guide to Injection Molding Automotive Parts
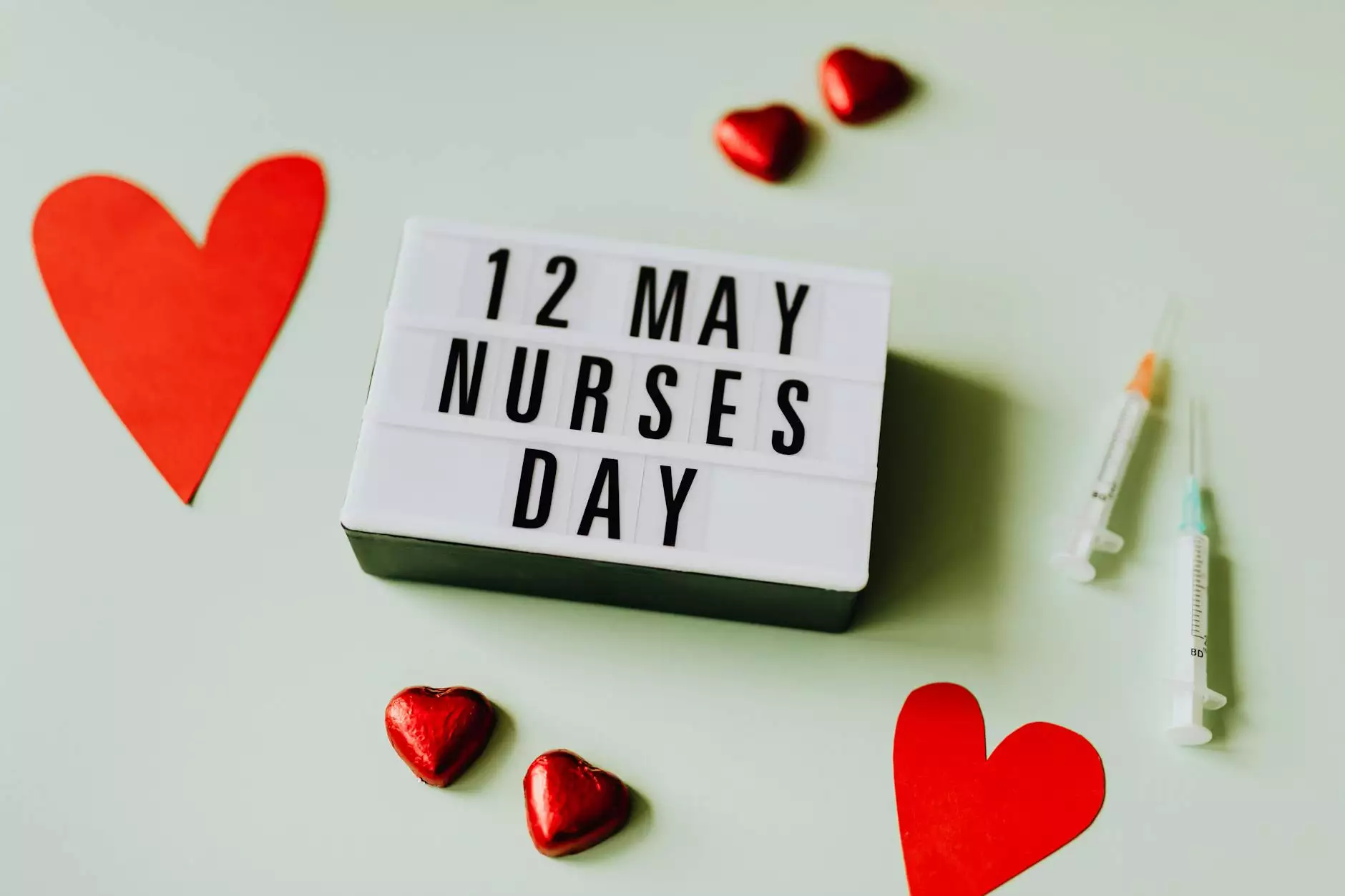
Injection molding is a highly efficient manufacturing process that is pivotal in the production of various automotive components. In this comprehensive guide, we will delve into the benefits, processes, applications, and future trends concerning injection molding automotive parts. Whether you are a manufacturer, supplier, or simply interested in the automotive industry, this article will provide you with the insights you need.
What is Injection Molding?
Injection molding is a manufacturing technique for producing parts by injecting molten material into a mold. The primary materials used in this process are polymers, metals, or glass. The hot material fills the mold, then cools and hardens to form the final product. This method is particularly important in the automotive industry due to its ability to produce parts with complex shapes and high precision.
Benefits of Injection Molding Automotive Parts
- Cost-Effective Production: The injection molding process allows for rapid production at a lower cost per part, making it highly economical for large-scale manufacturing.
- High Precision and Repeatability: Components produced through injection molding maintain consistent quality and dimensional accuracy, which is essential for automotive safety and performance.
- Material Versatility: A wide range of materials can be used in injection molding, including various types of plastics, metals, and composites, allowing for functional optimization of parts.
- Reduced Waste: Since the process utilizes a closed-loop system, it minimizes waste and enhances sustainability.
- Design Flexibility: Designers can create intricate components that meet specific performance criteria, making it ideal for innovative automotive designs.
Understanding the Injection Molding Process
The process of injection molding involves several key steps, which include:
1. Material Preparation
The chosen material, typically in the form of pellets, is dried and prepared for injection. This step is crucial to ensure that no moisture affects the final product's quality.
2. Melting the Material
The pellets are then conveyed into a heating chamber where they are melted at controlled temperatures suitable for the material's characteristics.
3. Injection into the Mold
Once the material is molten, it is injected into a pre-designed mold under high pressure. The mold is created to form the exact shape of the desired automotive part.
4. Cooling and Solidification
The injected material cools and solidifies within the mold. This step is crucial for defining the part's final structure and properties.
5. Ejecting the Part
Once cooled, the mold opens, and the finished part is ejected, ready for further processing or assembly.
Applications of Injection Molding in the Automotive Industry
Injection molding is widely used in various aspects of automotive manufacturing. Some common applications include:
- Interior Components: Dashboard components, controls, and trim pieces are often manufactured using injection molding due to their compatibility with various textures and colors.
- Exterior Parts: Light housings, bumpers, and body panels can be produced with high resistance to impact and weather, meeting automotive standards.
- Functional Parts: Structural components such as brackets, clips, and connectors that need high precision and durability are frequently manufactured using this process.
- Electrical Housing: Battery housings and other electronic component enclosures benefit from the protective characteristics of molded materials.
- Complex Engine Components: Parts like intake manifolds or specific engine covers can be efficiently produced to meet the high-performance demands of modern vehicles.
Choosing the Right Materials for Injection Molding Automotive Parts
Choosing the right material is crucial for the success of the injection molding process. Common materials utilized include:
- Polypropylene (PP): Known for its chemical resistance and ease of molding, making it ideal for interior parts.
- Polycarbonate (PC): Extremely tough and durable, often used for exterior components.
- Polyamide (Nylon): Excellent thermal and mechanical properties, commonly used for functional parts.
- ABS (Acrylonitrile Butadiene Styrene): Offers a balance of toughness and impact resistance, perfect for interior components.
- Glass-Filled Plastics: These enhance strength and rigidity, beneficial for high-stress applications.
Quality Control in Injection Molding
Maintaining high quality in injection molded parts is critical to the automotive industry. Various inspection methods and quality control standards are implemented:
- Visual Inspections: To identify defects and surface irregularities.
- Dimensional Checks: Ensuring parts meet stringent tolerances using gauges and measurement tools.
- Material Testing: Conducting tests for strength, durability, and chemical resistance.
- Process Monitoring: Continuous monitoring of the injection molding process to detect any deviations from quality standards.
The Future of Injection Molding in the Automotive Sector
As the automotive industry evolves, so does the technology behind injection molding automotive parts. The following trends highlight the future of this essential manufacturing process:
- Emphasis on Sustainability: The push for eco-friendly solutions is leading manufacturers to adopt biodegradable materials and recycling practices.
- Advanced Technology Integration: The implementation of automation and AI in the molding process is enhancing efficiency and precision.
- Customization and Fast Prototyping: Injection molding technology is becoming more accessible, enabling smaller manufacturers to produce custom parts quickly.
- Lightweighting: The trend towards reducing vehicle weight for better fuel efficiency is driving innovations in materials used in injection molding.
Conclusion
In conclusion, injection molding automotive parts is a cornerstone of modern vehicle manufacturing. Its numerous benefits, including cost-effectiveness, precision, and versatility, make it an ideal choice for producing a wide array of automotive components. As technology advances and sustainability becomes a pressing concern, the injection molding process will continue to adapt and thrive, solidifying its place in the future of the automotive industry.
For businesses focused on manufacturing and supplying injection molding automotive parts, leveraging these insights from deepmould.net can enhance strategies and drive innovation in your operations. Embrace the power of injection molding to stay ahead in this competitive market.